This refers to ultra-fine wires that are wound to create miniature coils and are used in the medical field to perform minimally invasive procedures. These procedures allow medical technicians to perform investigations in areas hard to reach and regions in the body that are normally inaccessible. Doctors can avoid disrupting normal functions of the body; they can also use these miniature medical sensors to perform cryo cancer treatment which is the freezing and heating of cancer tumors. These coils also help in increasing the life span of implants and help conserve energy consumption rather than using traditional methods of treatment.
The need for these coils has been steadily growing. However, there are very few manufacturers in the world with extensive experience and technical know-how that can produce these miniature medical sensor coils. Their awareness of this new technology is spreading, leading to the growth of new designers. However, designing these coils requires precise and designer equipment a well-equipped manufacturer can only do that.
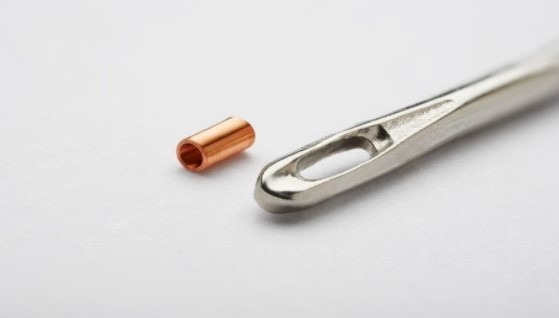
How does a manufacturer get started in using coils?
A manufacturer needs to show they can produce the micro-coils and insulate the ultra-fine wires. Heating these ultra-fine wires has adverse effects on them like heat degradation, oxidation and poor conduction. A manufacturer has to develop technology that does thermo-pressure bonding to solve the connectivity issues. This manufacturing process creates coils that do not solder are reliable, strain-free, corrosion-free, and cost-effective.
They make miniature coils using the state-of-the-art control system and micro-motions. They make coils out of copper and other metals and make wires that are five to ten times thinner than a human hair.
Requirements to manufactureminiature medical sensors
- Materials used have to be traceable from the quarry where the natural material was mined.
- The sensors need to be traceable- who was the manufacturer, the worker that made the device, and the date they made the device.
The design of the devices has to follow the client’s predetermined specifications. - The facility that manufactures the coils is subject to client inspection and must be ISO 13485 approved.
- Manufacturing of these coils must follow a strict set of codes, and high standards maintained during production. The whole point of these high standards is to ensure they make no faults during manufacture.
- A manufacturer needs to design and produce a state-of-the-art machinery to build custom coils since there are no ready-made machines that can make miniature coils.
These medical sensors have several applications which include:
- They are used in treatments like electrophysiology.
- They are used in monitoring and control active implants such as miniature pacemakers.
- Used to navigate the delivery of drugs to target radiation catheters.
- They can be used in measuring temperature since manufactures make them using technology that is thermo-pressure molecular bonding.
Manufacturing these medical sensors must be done by an experienced manufacture. They must also have state-of-art machinery and technical capability, since these devices are used to perform delicate medical procedures.
I’m a 20-something stay-at-home mother and wife. I have an amazing husband, a beautiful daughter, two loving dogs, and a lazy cat. I wouldn’t change my life for anything! I love to read, listen to music, cook and blog!
Speak Your Mind