Sterile injectable pharmaceuticals play a critical role in modern healthcare, delivering medications directly into the bloodstream for rapid and effective treatment of various medical conditions. Also, injectable sterilization methods encompass a range of techniques including steam sterilization, gamma irradiation, filtration, and aseptic processing, ensuring the elimination of microbial contaminants and upholding the safety and efficacy of injectable pharmaceuticals. Ensuring the sterility of these injectable products is paramount to prevent infections and adverse reactions in patients.
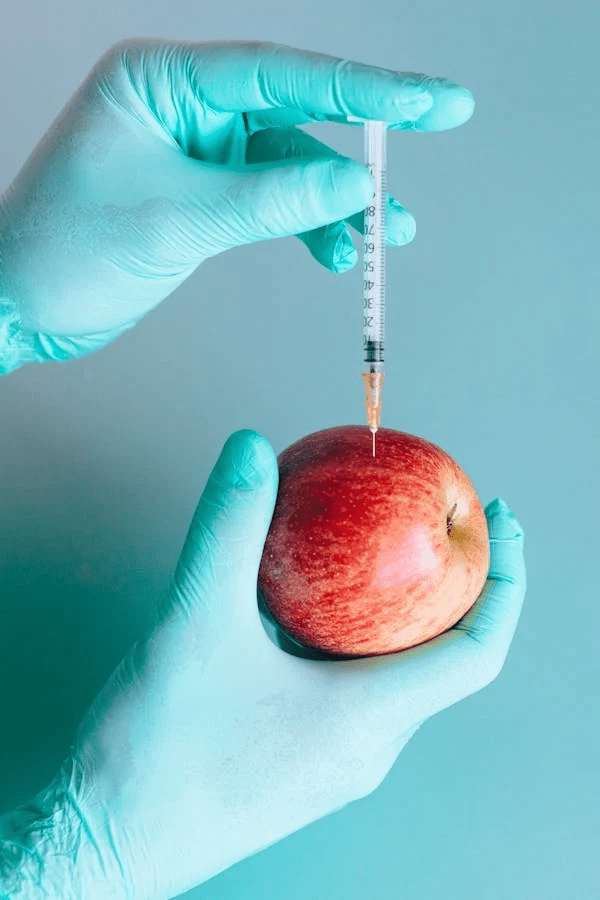
What are Sterile Injectable Pharmaceuticals?
Sterile injectable pharmaceuticals are medications that are free from viable microorganisms, ensuring their safety and efficacy when administered via injection. These products are typically supplied in vials, ampules, or prefilled syringes and may contain solutions, suspensions, or lyophilized (freeze-dried) powders that require reconstitution before use. Common types of sterile injectables include vaccines, antibiotics, anticoagulants
Manufacturing Process
The manufacturing of sterile injectable pharmaceuticals follows stringent guidelines and quality standards to ensure product safety and regulatory compliance. The process typically involves several key steps:
- Formulation: Active pharmaceutical ingredients (APIs) and excipients are combined in precise proportions to create the desired formulation. The formulation may be in the form of a solution, suspension, or lyophilized powder.
- Sterilization: Before filling, all components of the product, including vials, ampules, stoppers, and syringes, undergo sterilization to eliminate microbial contaminants. Sterilization methods may include steam sterilization (autoclaving), gamma irradiation, or filtration.
- Filling and Sealing: The sterile formulation is aseptically filled into individual vials, ampules, or prefilled syringes using automated filling equipment. Care is taken to maintain a sterile environment throughout the filling process to prevent contamination.
- Capping and Sealing: After filling, vials and ampules are capped with sterile stoppers or sealed with aluminum caps to maintain product integrity and sterility. Prefilled syringes are fitted with sterile plungers and sealed with caps or tip caps.
- Labeling and Packaging: Once filled and sealed, the sterile injectable products are labeled with relevant product information, such as name, strength, dosage form, and expiration date. They are then packaged into secondary packaging, such as cartons or trays, for distribution.
Sterilization Methods
Sterilization is a critical step in the manufacturing of sterile injectable pharmaceuticals to ensure the elimination of microbial contaminants. Several sterilization methods may be employed, depending on the nature of the components and the requirements of the final product:
- Steam Sterilization (Autoclaving): Steam sterilization is a widely used method for sterilizing heat-resistant components, such as glass vials, metal stoppers, and surgical instruments. The components are exposed to high-pressure steam at elevated temperatures (usually 121°C) for a specified duration to achieve sterilization.
- Gamma Irradiation: Gamma irradiation is a cold sterilization method that uses ionizing radiation to destroy microbial contaminants. It is commonly used to sterilize disposable components, such as plastic syringes, tubing, and packaging materials, without compromising their integrity.
- Filtration: Filtration is a non-destructive sterilization method that involves passing the formulation through sterile filters with pore sizes small enough to trap microbial contaminants. Filtration is often used for heat-sensitive components, such as protein-based formulas and vaccines.
- Aseptic Processing: Aseptic processing involves maintaining aseptic conditions throughout the manufacturing process to prevent microbial contamination of the product. This includes sterilizing equipment, maintaining a cleanroom environment, and implementing strict procedures for handling and filling sterile products.
ConclusionIn conclusion, sterile injectable pharmaceuticals are vital components of modern medical therapy, delivering medications directly into the bloodstream for rapid and effective treatment. The manufacturing of sterile injectables follows rigorous guidelines and quality standards to ensure product safety and sterility. Various sterilization methods, including steam sterilization, gamma irradiation, filtration, and aseptic processing, are employed to eliminate microbial contaminants and maintain product integrity. By understanding the manufacturing process and sterilization methods used in the production of sterile injectables, healthcare professionals and patients can have confidence in the safety and efficacy of these essential medications.
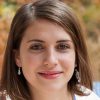
Hey welcome to my blog . I am a modern women who love to share any tips on lifestyle, health, travel. Hope you join me in this journey!
Speak Your Mind