Welding has been evolving ever since the time humans have learned how to connect metals by using heat. The rapid evolution of welding into its many forms was facilitated by technological breakthroughs in different eras. Welds can now be created from fires, electricity, chemical explosivity, or even atomic hydrogen.
There are several types and methods of welding for different type of work to be performed by welding but there is a common thing in all is SAFETY. Every type of welding requires safety measures from UV rays. According to Bestweldinghelmet.net, every must wear welding helmets and gloves while doing welding.
Many new welders are overwhelmed when they are trying to decide on which type of welding to learn first. Learn to weld to find out how to know about the different types of welding machines, tools and techniques available today to make an informed decision. Since the profession of welding is highly diverse while requiring years to master some branches, choosing a welding process that allows you to grow a favorable career path in welding should be done first. Visit Welding Near You to start your career in this field. Visit Welding Near You to start your career in this field.
We’ve compiled a list of the varying types of welding and their main uses in the industry.
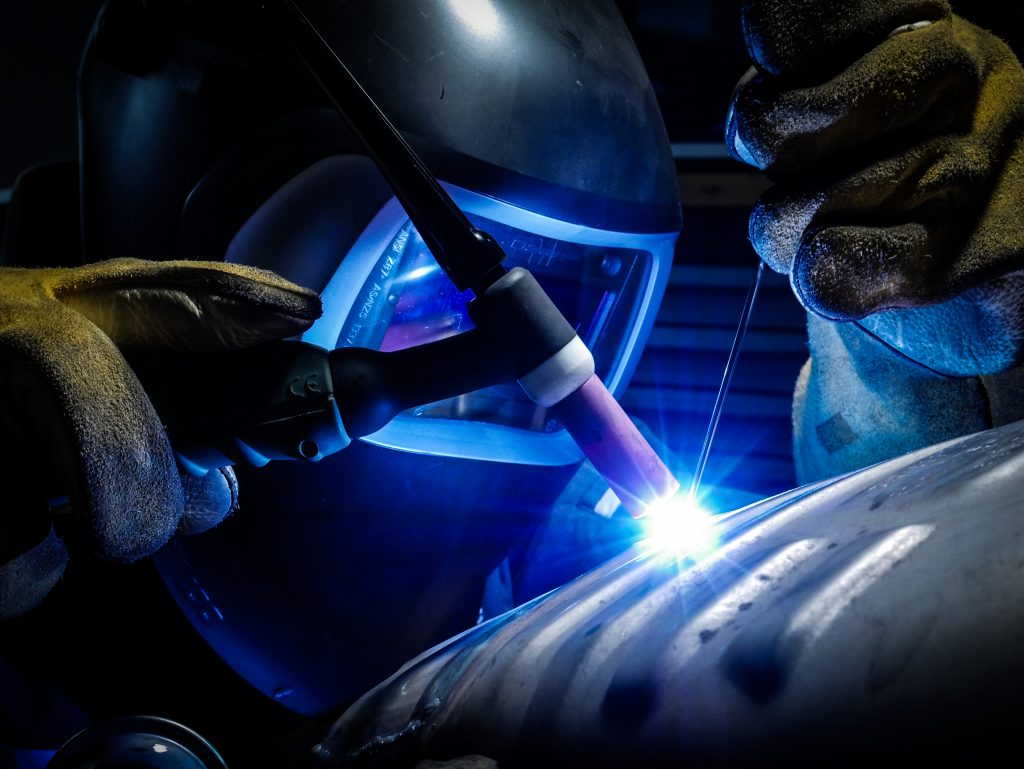
TIG
Tungsten inert gas welding (TIG) uses a rod of tungsten that isn’t consumed by heat or electricity. It’s one of the cleanest types of welding as it doesn’t require the usage of a metal filler to decontaminate and strengthen the welded joint; one can still be used if the welder deems it necessary. The welder has to be equipped with a gas tank that keeps the welding processes supplied by a constant flow of gas, making it not ideal for outdoor situations with a lot of wind and exposure. It’s often not a welder’s first choice because it requires a lot of experience to create visually appealing welds due to its precise nature.
MIG
Metal inert gas (MIG) is frequently picked as the first type of welding to learn by beginners due to its relative ease and straightforward process. The filler metal is always supplied to the weld in the form of a metal rod that the gas protects from interacting with other elements. The filler is fed into the weld from a spool, constantly melting along with the base metal to create a sustainable weld. It’s not hard to control the speed of the filler to adjust to different types of welds. Even though it’s not easy to weld using MIG outdoors, its flexibility and versatility make it perfect for many thicknesses.
FCAW
Flux-cored arc welding (FCAW) shares some similarities to MIG; knowing one well means that you can easily learn the other. The filler metal is in the form of a wire that’s fed from a spool as you weld. The main difference between MIG and FCAW is the type of filler metal used. The flux-core of the filler allows the creation of a barrier to protect the weld from outside elements without having to use a gas supply. This makes it more suitable for welds that are done outdoors or in a high-pressure environment, in addition to heavy metal welds.
Stick
The stick or shielded-metal arc welding method has been around for almost 100 years, but it has changed drastically in terms of variance and efficiency over the years. It’s popular because it’s quick, easy, and doesn’t require a lot of expenses. The main drawback is the splatter created by the weld which takes some time to clean up. It doesn’t require an external gas source because the filler metal is coated in flux material that can allow it to be used in harsh conditions like rain.
Plasma Arc
Plasma arcs can be compared to TIG arcs in the arc production process, but the main difference is the small size of plasma arcs. The temperatures achieved through ionized plasma are much higher, reaching temperatures up to 28,000 degrees Celsius. The gas inside the wad is converted into high-powered and electrically conductive plasma through pressurization and ionization. The higher temperatures make it easy not to use any filler metal during the weld. It requires extra proficiency and experience because plasma arcs require a lot of precision.
Explosion Welding
The process of explosion welding was discovered during the Second World War. It allowed for the fusion of two unlike metals that wouldn’t fuse under normal welding conditions. It uses chemical explosions to accelerate metals at a very high speed, resulting in solid-state welding products. It’s most commonly used to add corrosive-resistant properties to steel through the incorporation of silver, nickel, brass, or titanium metal alloys.
Electroslag Welding
This welding process is done on two thin metal plates to conjoin them vertically. Unlike most other types of welds that weld joints, the welding arcs in electroslag welding are applied to the whole edges of the plates. The filler metal is copper being continuously fed into a guide tube; copper is chosen for its high electrical conductivity. The weld happens slowly through connecting electricity to the edges, causing it to create the outlined seam.
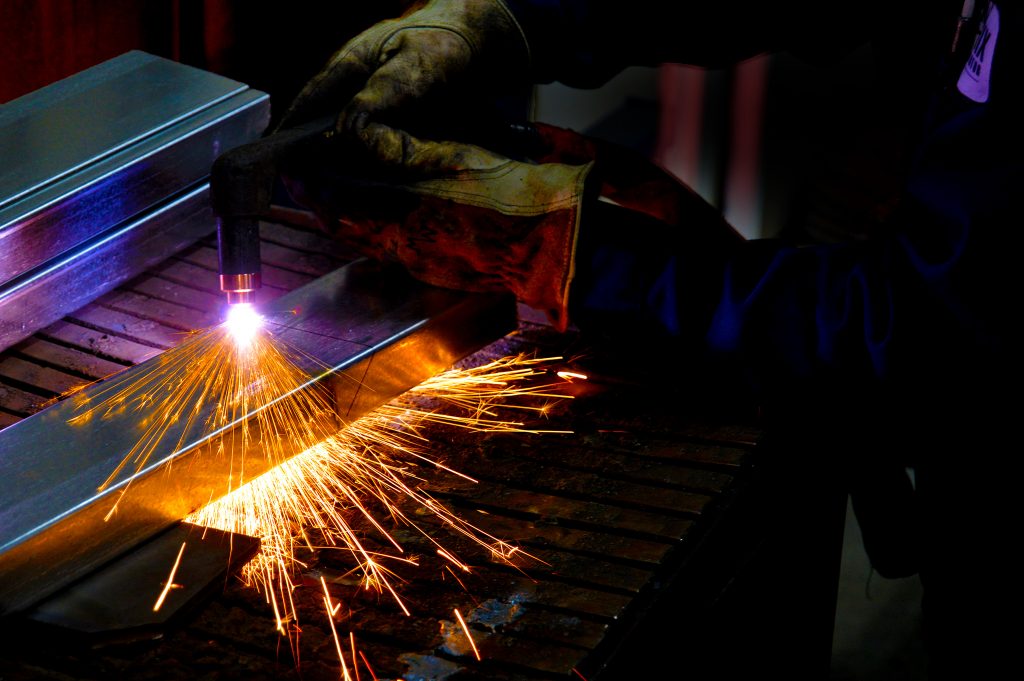
It’s not uncommon to be interested in more than one type of welding process to widen the range of jobs that can be done. It’s best to start with similar types of welding that can be used in different conditions before you move up to more intricate ones. It may also be of help to watch as many online tutorials as time allows you before you begin practicing.
I’m a 20-something stay-at-home mother and wife. I have an amazing husband, a beautiful daughter, two loving dogs, and a lazy cat. I wouldn’t change my life for anything! I love to read, listen to music, cook and blog!
Speak Your Mind